Plastic bottles made of PET preforms involve all aspects of our lives, such as mineral water bottles, tea beverage bottles, soda carbonated beverage bottles, edible oil bottles, cosmetic bottles, detergent bottles and candy cans, etc., and are widely used in the market. Plastic packaging products, how to do it well? To share with you based on your own manufacturing experience:
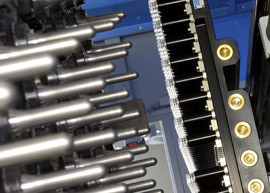

PET preform mould price
1. Our moud core and cavity are made of S136 steel material after heat treatment to ensure the hardness and life span, and the maximum number of moulds is 500.
2. The hot runner system with German heating elements makes the plastic flow faster in the molten state, saves materials, and effectively guarantees the quality stability of plastic products.
3. The benefits are determined by quantity, such as mineral water bottles, soda carbonated beverage bottles, tea beverage bottles, etc. The number of mould cavities determines the benefit, and we achieve a maximum of 128 cavities.
PET preform mould price
4.
PET preform price: It is very important to save costs for users. The mould should be designed with interchangeable parts, such as screw mouth, weight, cavity, core, etc., so that a pair of moulds can be replaced by different inserts. Bottle weight and shape.
5. The clamping structure adopts a double-cone positioning design, which can avoid undesirable defects such as flash, different sizes, and eccentricity after moulding.
6. Use foreign advanced processing equipment to process the preform mould with high precision. In addition, bridge type three-coordinate measuring instrument and articulated arm measuring instrument are used to control the precise size of the mould.
7. After the mould manufacturing is completed, we will carry out a series of running inspection tests in accordance with the company's quality standards, and only after all the tests meet the requirements can it be shipped.
8. We will provide spare parts, such as core/cavity inserts, and other replaceable mould parts, so that damaged parts can be replaced quickly.
Latest blog posts
Custom molds injection molding
Custom molds injection molding is a manufacturing process that involves creating custom molds to produce plastic parts. Injection molding is a popular technique used in various industries such as...
Plastic injection molding companies
Plastic injection molding is a manufacturing process that involves injecting molten plastic into a mold to create a wide range of plastic products. From car parts to medical devices and household items, plastic injection molding is used to create a variet
PET Preform Injection Moulding Machine
PET preform injection molding is a manufacturing process that is used to create PET (polyethylene terephthalate) preforms that can be later blown into bottles, jars, and other containers. This process...
You may like
Four aspects that determine the accuracy of thin-walled injection molded parts
The application of plastic parts is becoming more and more extensive, from simple tableware. kitchenware to complex mechanical parts. However, for plastic parts with high...
Several aspects that need attention to reduce the degree of wear of injection molding machine screw
Several aspects that need attention to reduce the degree of wear of injection molding machine screw, Injection molding machine screw for a long time in high temperature, high pressure...
Preventing screw slippage on injection molding machines
For hygroscopic materials (such as nylon), high resin moisture content can also cause screw slippage. Improper drying can significantly reduce the viscosity of the material and cause...
Teach you how to reduce the processing cost of injection moulds
Reasonable and effective reduction of the processing cost of injection mold can effectively improve the economic efficiency of enterprise production, can effectively reduce the production...